
What’s new in NX for Manufacturing (December 2020)
The latest version of NX for Manufacturing, a comprehensive software portfolio for part manufacturing, is now available.
Our Digital Manufacturing team has implemented many new software capabilities, enabling programming automation and advanced manufacturing methods.
NX’s new release is packed with new operations and powerful enhancements for CNC programming, additive manufacturing, CMM inspection programming, and manufacturing data management.
Read more about how you can accelerate part manufacturing using the new capabilities in NX software.
NX CAM
Planar Deburring, a new machining method, helps you automate the programming of one of the most-used operations – corner chamfering. It can slash your programming time by up to 95%. NX CAM software automatically recognizes parts’ edges (modeled or unmodeled) and creates optimized toolpaths to machine the required chamfer size. You can also specify a size range for holes to be skipped for more precise control of the toolpaths. Additionally, Planar Deburring tracks already chamfered corners, eliminating re-cutting and enabling efficient 3+2 machining.

Planar Deburring in NX CAM automatically generates toolpaths to machine all the part edges
Adaptive Milling, NX CAM’s high-speed machining cycle, has been expanded to support boundaries used for programming of prismatic parts. This highly efficient roughing strategy, which enables deep cuts and high cutting speeds, replaces the Trochoidal operation for faster machining. The advanced Adaptive Milling method maintains consistent chip load that extends tool life, while reducing roughing cycle time by up to 60%.

Adaptive Milling, NX CAM’s high-speed roughing cut pattern, is now available in Planar Mill operation that’s used for programming prismatic parts
Pinch Turning, a new advanced cutting method, enables simultaneous machining by two opposing cutting tools. It balances the cutting forces of two opposing cutting tools and minimizes parts deflection, allowing deeper cuts. Additionally, one of the tools can perform a semi-finishing operation while the other, slightly trailing the opposing tool, performs the finish operation. The new turning operation delivers higher productivity and accuracy.

The new Pinch Turning operation in NX CAM provides two modes for faster machining:
– In Balanced mode, the opposing tools are aligned and cut the same diameter
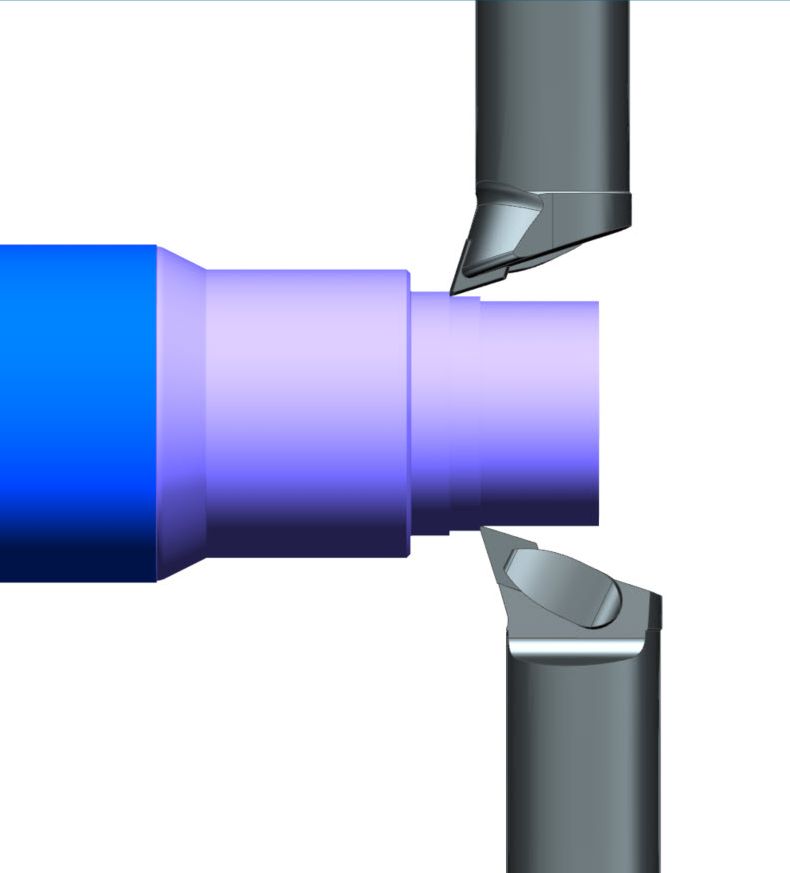
– In Merged mode, one of the tools trails the opposing tool and the tools cut different diameters
Productivity enhancements help you quickly define the machine setup, allowing you to focus on high-value programming tasks. You can now reduce setup time by quickly creating blanks from solids that you can accurately position in reference to the part models. In addition, the new interactive creation of Machining Coordinate System (MCS), allows you to quickly define the MCS origin on the blank.

Quickly define solid blanks and Machining Coordinate Systems (MCS) in the new version of NX CAM
NX Additive Manufacturing
Continued investment improves the NX Additive Manufacturing solution for multi-axis and planar printing.
With new coating, slicing, and supports enhancements, it is easier than ever to set up your build tray and to apply coatings to 3D surfaces. New coating capabilities support easier programming of parts with multiple plied layers, while CLI slicing gives customers support for a wider range of print technologies.

NX Additive Manufacturing allows creation of multiple plies on forms for strength and light weight
Furthermore, new support profiles and traceability save time, ensure compliance with company standards, and allow for better management of support attributes.

Support profile assignment in NX Additive Manufacturing is now integrated within the regular build preparation workflow
NX CMM Inspection Programming
Tactile scanning paths programming automates the creation of inspections paths on planar sections of parts. NX CMM Inspection Programming generates optimized, high-speed inspection paths using only the planar face as input, eliminating the need to create auxiliary geometry to define the inspection path. The new enhancement helps you quickly create tactile scanning paths that are being increasingly used to inspect parts with Geometric Dimensioning and Tolerancing (GD&T) data.

NX CMM Inspection Programming automatically generates tactile scanning paths on planar faces
Enhanced 5-axis inspection programming functions for Renishaw Revo enable precise control of the tilt and advance angles of inspection paths. Programming of 5-axis inspection paths can be extremely challenging using traditional methods. The new controls simplify the programming of parts with complex geometries, such as airfoil sections.

NX CMM’s enhanced 5-axis inspection programming functions for Renishaw Revo provide precise control of the tilt and advance angles
Manufacturing Data Management
The seamless integration between NX and Teamcenter enables efficient part manufacturing data and process management, using a single source of data.
CNC programmers can retrieve manufacturing resources, such as cutting tools, fixtures, and machine models managed in the Manufacturing Resources Library (MRL).

Active Workspace’s modern interface enable you to drag manufacturing resources from the Manufacturing Resource Library into NX CAM
Using Active Workspace embedded in NX, programmers can now drag resources from the MRL directly into NX CAM. The modern interface allows you to quickly define an accurate digital replica of your machine setup, so you can efficiently program and manufacture high-quality parts for your industry.