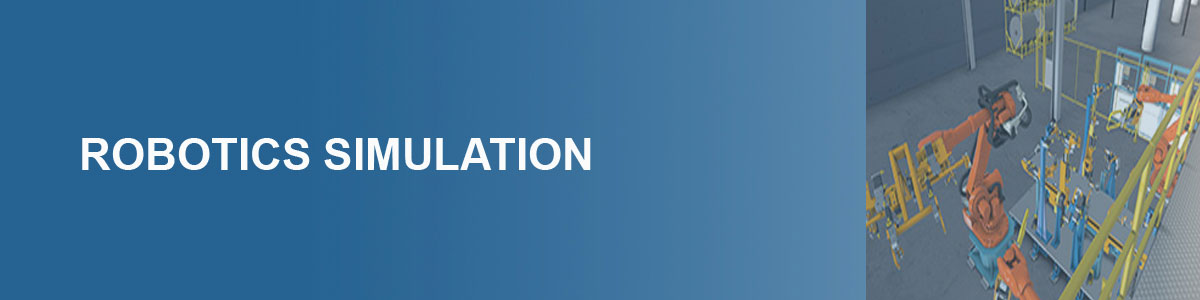
Robotics & Automation Simulation
Offline Program Robotics & Automation
Design, simulate and offline program operations utilizing robotics and automation.
Tecnomatix robot simulation software and automation programming solutions enable work in both data-managed and file-based environments for the development of robotic and automated production systems. These tools address multiple levels of robot simulation and workstation development, from single-robot stations to complete production lines and zones.
Using collaborative tools, you can enhance communication and coordination among manufacturing disciplines, enabling smarter decision-making. This allows you to bring automation systems online much faster and with fewer errors.
Robotics & Automation Programming
Leverage robotics and automation equipment to gain and increase flexibility for more complex manufacturing operations and to boost overall production efficiency.
Across all major industries, market pressures and structural costs are requiring manufacturers to build more automation and increased flexibility into their production facilities. Individual plants need to increase the number of products they can build, while exceeding their current quality targets and optimizing their shop floor footprint. Manufacturers must rely, more than ever, on robotics and robot simulation software automation systems to gain flexibility for more complex manufacturing operations and to boost their production efficiency.
Automation & Robot Simulation Software
Engineer and optimize robotic and automated production systems using 3D robotic workcell design, simulation, and offline programming.
With Tecnomatix® software’s robotics and automation simulation solutions, you can work in both data-managed and file-based environments for the development of robotic and automated production systems. These tools address multiple levels of robot simulation and workstation development, from single-robot stations to complete production lines and zones. Using collaborative tools, you can enhance communication and coordination among manufacturing disciplines, enabling smarter decision-making. This allows you to bring automation systems online much faster and with fewer errors.
Design Complete Workcells with 3D Kinematic Models
Tecnomatix Process Simulate Robotics and RobotExpert software provide the tools necessary for the design and validation of manufacturing processes in a dynamic and highly visual environment where manufacturing engineers can author, re-use, validate and optimize manufacturing process sequences with realistic behavior using fully kinematic 3D models. These solutions support a variety of robotic and automation processes allowing for early validation of automation concepts virtually and the simulation, offline programming and commissioning of complete production systems.
Plan, Simulate and Optimize Robotic Operation Paths
Tecnomatix robot simulation software and automation simulation solutions give you the power to simulate complete manufacturing cells and systems allowing you to design and validate collision-free robotic paths and optimize their motion and cycle times, using both time-based and event-based simulation methods. Dedicated tools for various robotic applications, such as resistance spot welding, arc welding, cutting, spraying and pick-and-place operations further enhance your ability to define the correct motion for the robots and automation in your systems.
Program Robots and Automation Completely Offline
Tecnomatix software’s offline programming solution for Process Simulate and RobotExpert enables accurate simulations of robot motion sequences and the delivery of production-ready programs to and from the shop floor. Interfaces to all major industrial robots allow controller-specific motion planning, simulation and program execution. Detailed information, including motion and process attributes, can be added to the generated robot paths for the creation of complete programs downloaded to the real controller, resulting in more efficient offline programming.